会員向け情報
研究室紹介
3Dプリンター(砂積層)工法を利用した新しいモノづくり
近年3Dプリンター技術が製造業に革命をもたらしています。
弊社は2007年よりプリンター技術を導入、活用し3次元砂型積層造型を取り入れた革新的な鋳物作りに取り組んでいます。以下3次元積層技術と試作業務への利用状況について紹介します。
1.はじめに
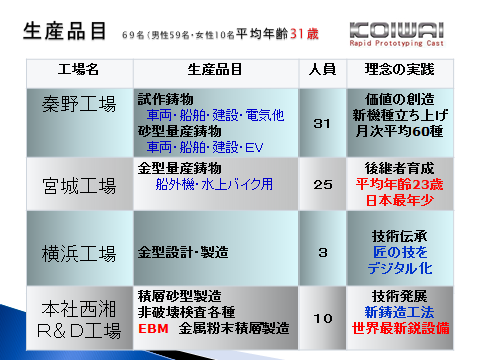
株式会社コイワイは、神奈川県小田原市に本社西湘R&Dを構え、秦野砂型工場、横浜金型工場、宮城金型量産工場の4事業所からなっている
弊社の営業品目は、
- RP 砂型積層工法による各種鋳物の試作鋳造品・並びに積層砂型の製造販売 【適用材質】:アルミニウム・マグネシウム・鋳鉄・ダクタイル鋳鉄・ニレジスト耐熱鋳鉄・鋳鋼・ステンレス鋼・CAC等銅合金
- 金型鋳造による量産品の製造
適用材質:JIS 規格アルミニウム各種、その他 - EBM 金属粉末溶融積層工法
適用材質:Ti6Al4V :CoCr Alloy - 鋳造品をはじめとした各種機械加工
- 鋳造用金型・樹脂型製作
- 3 次元CAD によるモデリング業務
- CT による受託撮影、非破壊検査、接触式3次元測定
- リバースエンジニアリング
弊社は3 次元CAD によるモデリング、鋳造方案設計、樹脂型・金型製作、RP 砂型積層工法による各種鋳物の試作、製品加工(協力メーカー様委託)CT による受託撮影、非破壊検査
一気通貫で手掛けている(図1)。
積層造形(3Dプリント工法)とは
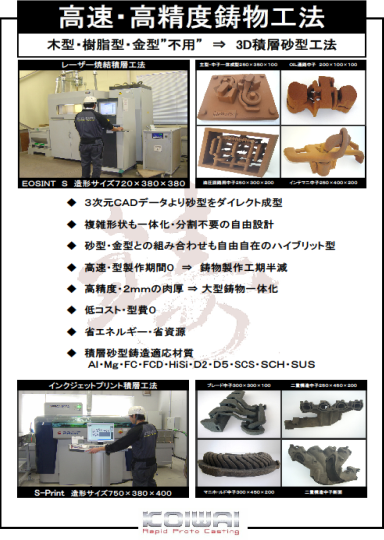
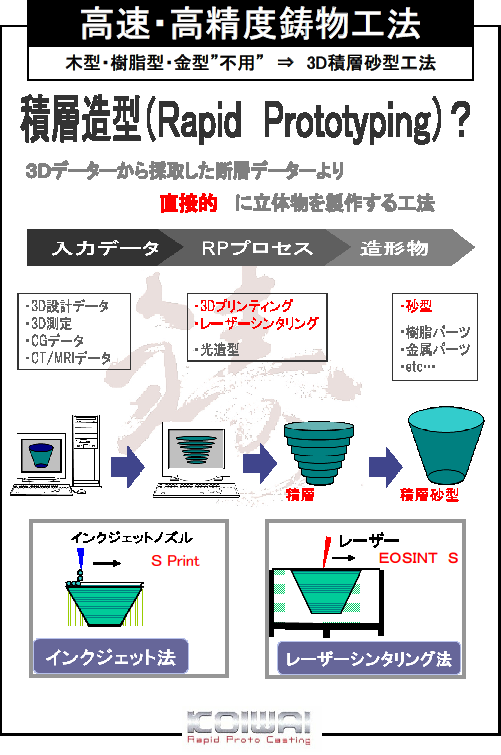
積層造形の原理は製品の3 次元形状を薄い層にスライスし、何らかの方法によりこの薄い層を自動的に製作して、これを繰り返すことにより3次元形状を積層的に造形するものである(図2)
弊社はレーザー式砂積層【2機】、インクジェット式砂積層【3機】、EBM(エレクトロビーム溶融積層)【1機】 3種の積層工法を導入し2013年3月現在6台の積層装置を稼働している。(図3)
■ EOS-S750(図4独EOS社製EOSINT-S750)
レーザー焼結積層法、セラビーズ100%(量産時はシェル金型工法同等)、砂粒径50μm、積層ピッチ200μm、約1 時間で約30mm積層可能。1次レーザー積層後にオーブンでの2次焼結があります。生産スピードは最長で2日間。製造できる最大サイズは730×380×380 mmとなります。
面粗度は量産時の熱硬化式シェル工法と同等になります、用途は油や水通路等の小径で複雑な形状を得意とする。製品例ではターボチャージャーのベアリングハウジング等があります。
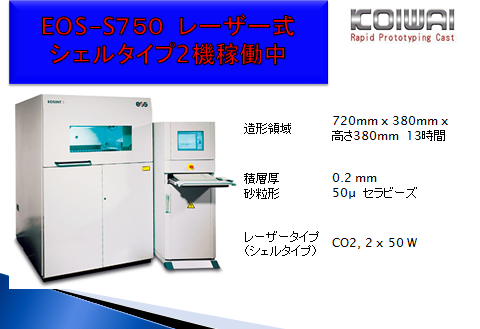
■ S-Print(図5、㈱EX_ONE社製)
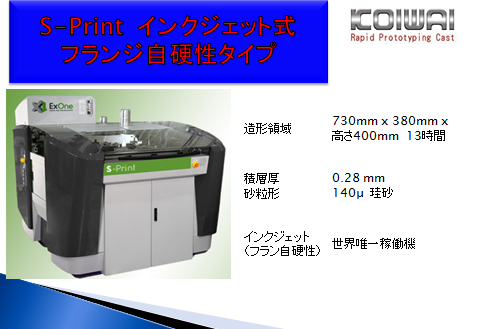
インクジェットプリント工法、使用する砂は硅砂100%(量産時はフラン自硬性工法同等)。粒径は140 μm、積層ピッチは280 μm、1 時間で約30mmの積層が可能。積層終了後3時間硬化後には鋳造が可能。生産スピードは1日の製造最大サイズは760 × 360 × 380mm。面粗度は砂の特性上140 μm 以上に粗い。研究用に使用
上記2種の積層装置の造形領域は約700×330×380となり砂型サイズには小型となり試作の範囲であった。
近年の積層装置の大型化により2012年S-Max(㈱EX_ONE社製、造形サイズ1800×1000×700)の導入により大型鋳物製品並びに小物多品種少量並びに量産工法に進化していく。
インクジェット式大型積層装置(図6)
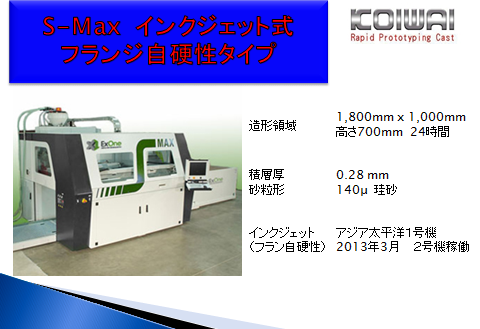
S-Max積層装置は大型鋳型の積層は勿論可能になるが、弊社の場合月次平均40種近くの試作を手掛けている場合、多品種対応(図7)に役立てている。図中の色の違いは全て別砂型になり、主型・中子が混在しています。
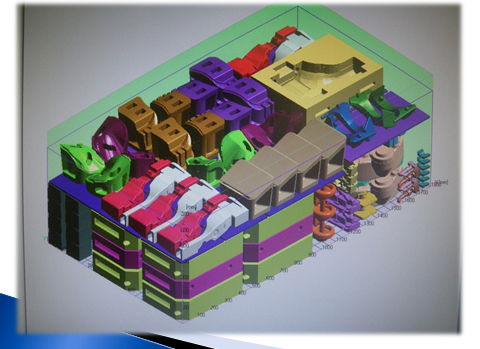
3.弊社の積層装置導入の背景(図8)
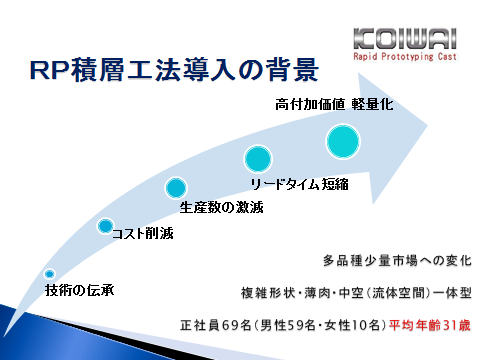
鋳造業に係わる社会環境の変化、市場性、技術の伝承等多くの問題を弊社は積層工法を活用することにより解決しています。
最大の要因は鋳造技術の伝承に有ります。
2013年3月現在正社員数69名平均年齢31歳は業界でも若い部類となります。若い=鋳造経験者が少ないという欠点も備えます。
現在・未来の平成社会人の技術力で鋳造技術の伝承を考え導入に至っています。
2014年度新入社員は4名、総正社員数73名、平均年齢30.3歳となります。平成社会人のデジタルに関するセンスは生まれながらに培いコイワイの積層工法には大変役立てています。
昭和社会人の場合、最新の携帯電話、通信機器やPC等を購入した場合間先ず説明書を開いてみるのが当たり前と思いますが、スイッチをONして、見て、触れて覚えるのが平成社会人ではないでしょうか。
積層レイアウト等のセンスは格段に彼ら、彼女らに軍配が上がります。
4.積層工法導入の相乗効果
2007年レーザー式砂積層装置EOSINT-S750の導入に始まり、毎年増設してきました。(図9)
従来鋳造業の抱える問題解決に積層装置が活躍するとは思いもよりませんでした。積層工法を導入して得られた効果は以下の通りです。
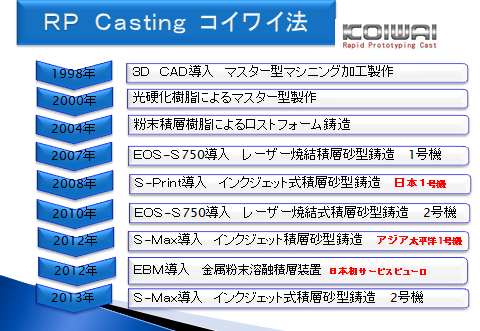
■ 積層工法で得られた効果(図10)
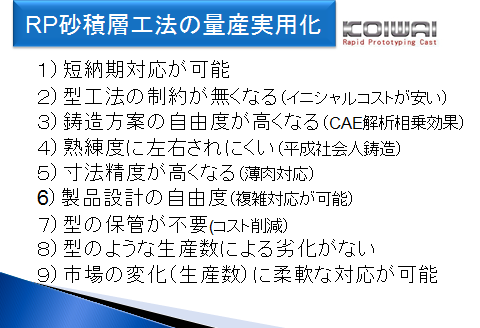
1)省エネルギー、省資源
中子はほとんど型製作、加工しないため型加工点数が約80%削減。中子型がないため、砂型中子製造スタッフも不要で大幅な経費削減に繋がる。
2)樹脂型・金型が不要
砂型鋳造には、型メーカーによる型供給が必須であったが、RP工法の採用により難易度の高い型が不要となり、型メーカーが悩む薄肉・複雑形状・後継者育成問題等が解決された。
3)砂型鋳造技術の伝承
従来は主型、中子と工法別に専門的な製造技術が必要であった。積層工法の場合従来型工法による制約が無くなり、分割中子等の製作が不要となり精度や中子等の補強対策などの問題も解決でき、デジタルデータによって技術が継承されるようになった。
4)方案技術の伝承
鋳造方案には、鋳巣対策、湯流れ対策、砂込め易さ、砂型組み付け対策など様々な必要対策や工法的制約が存在する。例えば複数の冷やし金をRP一体内製鋳造で製作できるため、従来のように砂型造型時に冷やし金がずれてチル効果を発揮できないような不具合も少なくなり、RP 中子を使用することによって多くの問題が解決され、不良率が大幅に削減される。
鋳造現場でのRP工法の効果は大きいが、それ以上に新規発注時のスタート方案や型構成設計などの短納期対応が著しい。鋳造経験がないモデリングスタッフに自由にモデリングさせ、その1/2 モデルをRPで製作し、実際に組んでみる。鋳造経験がない人が組めるのであれば鋳造現場でも問題なく組めると予想される。鋳造経験者の固定概念にとらわれることなく自由な発想で鋳型製作を行う。これによって鋳造技術未経験者でも平成生まれの鋳型製作技術者が日々誕生しています。
弊社の積層鋳造工法は、木型・樹脂型・金型が不要で3 次元CAD から直接砂型を積層造形する工法です。3 次元CAD データより砂型をダイレクトに成型し、複雑形状にも一体成型が可能で高速、高精度、低コスト化が実現できる。マスター型が不要になることで、省エネルギー、省資源にも対応した次世代鋳造技術である。
更なる革新
ダイレクト金属積層EBM(電子ビーム金属粉末溶融積層工法)(図11)
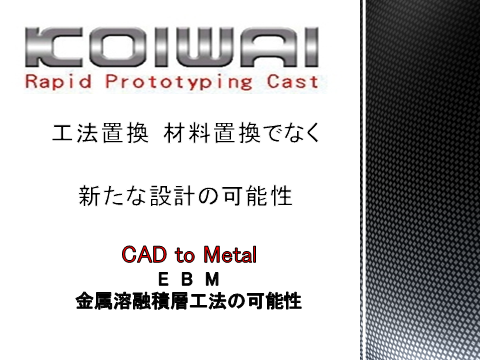
CADtoMetal
コイワイの進化は未だ始まったばかり