誰でも分かる技術
誰でも分かる鋳物基礎講座
生型砂とベントナト
3. 生型砂の変化(混練から造型まで)
3回目の最終回になりますが、今回は生型砂の変化に的を絞って纏めます。
混練直後の排出砂と造型直前の(コンベア等で搬送された)砂を握って触感の違いを感じ、不思議に思ったことはありませんか?混練直後の排出砂にはベタツキ感があり、造型直前の砂はベタツキ感が収まっています。 その理由を図1、21)を用いて説明します。
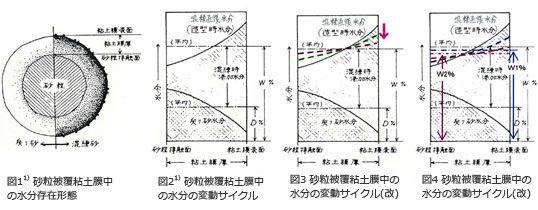
図1の左半分は戻り砂の砂粒で注湯熱により粘土膜表面の水分は蒸発し、砂粒接触面付近には若干の水分が残っています。水分含有の多い部分が黒点(∴)で表されています。この水分分布をグラフで表すと図2になり、2つの曲線のうち下が「戻り砂の水分」を示し、砂粒接触面での水分が高く、粘土膜表面側に移るにつれて低くなり、平均水分はD%であらわされています。次に図1右半分は「混練直後の砂の水分」で、その含有水分は図2の上の曲線から分かるように、粘土膜表面の水分が高く、砂粒接触面に近づくほど低くなり、「戻り砂水分」とは逆の勾配になっています。この砂の平均水分はW%です。混練時の添加水分は(W-D)%となります。
川の水が高い方から低い方に流れるように、図2の「混練直後の水分(粘土膜表面の水分が高く砂粒接触面が低い)」は、コンベアで搬送、乗継ぎ、エアレータ、造型ホッパーそして切出され、造型される迄に水分勾配がゆっくり均等化され,図3の緑色破線で示されるように変化します。搬送距離が長く、乗継ぎ回数が多いと紫色破線のように更に均等化が進み、サンドビン等で貯蔵すると平均値(W%)近くまで均等化します。混練直後の水分W%(以降、W=3.5%と仮定します)は変化しませんが、黒色→緑色→紫色→平均と変化するにつれて、粘土膜表面の水分は低下(桃色矢印;↓)します。この表面水分の低下によって、造型直前の砂のベタツキ感が収まります。そして、ベタツキ感(触感)の変化と同時にCBも変化(混練直後のCBに対して造型直前のCBが低下)し、造型性も変化します。このCB低下を乾きと表現することもあります。但し、今までの説明の様に、W%が混練直後から造型直前まで3.5%のまま変化の無い砂は理想に近いです。
しかし、多くの工場では、混練直後の水分W=3.5%の場合、造型直前の水分は3.2~3.4%程度に低下してしまいます。混練直後 (または、混練前) の砂温は、殆どの場合、気温より10~30℃程度高いのが実状です。砂温が高いと、粘土膜表面の高水分と砂粒接触面の低水分との間の水分均等化と同時に、粘土表面の水分は蒸発(気化潜熱によって砂温は低下)し、図4青色破線のように造型直前の水分が低下(W1)します。混練直後から造型直前までに搬送距離・時間が同じと仮定しても、砂温と気温の差が大きくなると、図4の青色破線から紫色破線のように砂粒表面の水分が更に低下(W2)し、造型直前の砂はCB低下が大きくなるので、気温との温度差増大にも注意する事が大切です。仮に造型直前砂のCB低下が大きくても、その低下幅が一定(正常稼動時:混練直後から造型直前までの砂搬送/待機時間が一定)なら管理できますが、湯待ち・チョコ停・設備故障等のライン停止が発生する実際のラインの場合は停止時間によりCB低下幅が変わり、CB管理範囲幅以下の値になることも多々あります。
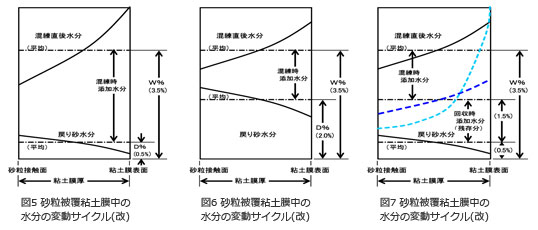
では、造型直前までのCB低下を少なくするためにはどうすれば良いかと言うと、①「砂温を下げる」(砂温と気温の差を出来るだけ少なくする)、②「戻り砂の水分D%を高くする(図5、6参照)」、③「充分で適切な混練時間の設定」により、砂粒接触面と粘土膜表面の水分差を小さくする (混練不足の場合、砂粒触面と粘土膜表面の水分差が大きくなる。過混練では砂が加熱され逆にCB低下要因になる)。更に④「充分な寝かせ」です。①の「砂温を下げる」と②の「戻り砂の水分を高くする」はともにS/M比(サンド/メタル比)に関係しますが、昨今できるだけ小さなS/M比(鋳物原価低減の為)で製造します。結果、戻り砂は高温・低水分となり、回収系でより多くの加水が必要になります(加水方法:ベルトコンベン上での散水、加水ドラム、バイブラドラム、MIA+クーリングドラム式など)。図7は加水後の砂の状態が示し、水色破線は散水しただけの場合で、粘土膜表面の水分が高くべたつきやすく棚吊り等の懸念があります。加水部をよく攪拌・反転・乗継ぎにより出きるだけ水分を均等化し、更にサンドビンで充分寝かせることが必要です(青色破線のように更に均等化が進む)。また、図7から戻り砂が0.5~1.0%程度の低水分のまま加水しない時は、寝かせ効果が期待できないことも分かります。
最後に生型砂性状・管理範囲は、十人十色ならぬ十社十色ではないでしょうか。種々の砂性状・管理範囲がありますが、不具合のある鋳物が発生しない砂性状がそのラインに適した砂です(その他の要因は造型機、方案等)。そして、砂性状のバラツキが少なければ、鋳物の品質のバラツキも少なくなり、原価低減につながるのだと思います。
3回連載した事が読者皆様のお役立てば幸いです。御一読有難うございました。
参考文献
1. 金森正弘:研究報告38「システムサンドの安定化に関する研究」(1985年 日本鋳物協会)